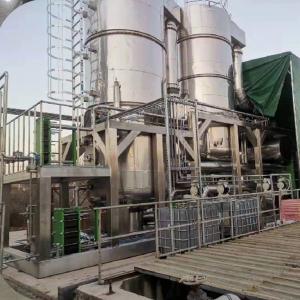
Add to Cart
The application of MVR evaporator technology in China has become increasingly mature. Compared with traditional evaporators, MVR evaporators have many incomparable advantages, so they are increasingly used in China. We have rich experience in both process design and electrical control, and the equipment success rate has reached 100%.
Definition and Principle:
MVR (Mechanical Vapor Recompression) evaporator is a mechanical vapor recompression evaporator, which is an efficient and energy-saving evaporation equipment. Its core principle is to compress the secondary steam generated by the evaporator through a compressor, increase the pressure and temperature of the secondary steam, and then send it back to the heating chamber of the evaporator as heating steam, and use it as a heat source to heat the liquid to continue evaporating the water in the liquid. In this way, except for a small amount of external fresh steam required during the equipment startup phase, there is almost no need for additional steam supply during normal operation, and the evaporation process is mainly achieved by recycling and reuse of steam.
Main components:
Evaporator body:
Including heating chamber and evaporation chamber. The heating chamber usually adopts the structure of shell and tube heat exchanger or plate heat exchanger. In the shell and tube heat exchanger, the liquid flows inside the tube and the steam channel is outside the tube. The heat of the steam is transferred to the liquid in the tube through the tube wall, causing its temperature to rise and boil and evaporate. The evaporation chamber is used to separate steam and concentrated liquid. Its design needs to ensure that the steam can be discharged smoothly while preventing droplets from being entrained by steam.
Compressor:
This is a key component of the MVR evaporator, responsible for compressing the secondary steam generated by the evaporator. There are many types of compressors, such as centrifugal compressors, roots compressors and screw compressors. Centrifugal compressors are suitable for processing large flows of steam and have higher efficiency; roots compressors and screw compressors are more suitable for processing small and medium flows of steam, and can adapt to different steam pressure and flow changes to a certain extent.
Separator:
It is mainly used to completely separate steam and concentrate. It uses gravity, centrifugal force or a combination of both to achieve separation. The gravity separator has a simple structure and relies on the density difference between steam and concentrate for separation; the centrifugal separator uses the centrifugal force generated by high-speed rotation to make the steam and concentrate move in different directions under the action of centrifugal force, thereby achieving efficient separation.
Condenser (may be required for some systems): When the non-condensable gas generated in the system needs to be discharged or part of the steam needs to be condensed, the condenser will be used. The condenser usually adopts a water-cooled or air-cooled structure. The water-cooled condenser uses cooling water to take away the heat of the steam and condense it into liquid; the air-cooled condenser uses air as a cooling medium to achieve the condensation of steam.
Pump system:
Includes feed pump, circulation pump and discharge pump. The feed pump is used to transport the raw liquid to the evaporator; the function of the circulation pump is to circulate the liquid in the evaporator to ensure that the liquid can be fully heated and evaporated, especially in some forced circulation MVR evaporators, the role of the circulation pump is more critical; the discharge pump is used to discharge the concentrated liquid from the evaporator.
Control system:
Used to monitor and adjust various operating parameters of the MVR evaporator, such as temperature, pressure, flow, liquid level, etc. The parameter information of each part is collected through sensors, and then the compressor, pump, valve and other equipment are automatically controlled according to the preset control strategy. For example, when the pressure or temperature in the evaporator deviates from the set value, the control system can adjust the speed of the compressor or the opening of the valve in time to ensure the stable operation of the evaporator.
Workflow:
Feeding stage:
The raw liquid is transported to the heating chamber of the evaporator through the feed pump. During this process, the feed speed can be adjusted according to the processing capacity of the evaporator and the properties of the liquid. At the same time, the control system monitors parameters such as feed flow and liquid level to ensure the stability of the feeding process.
Evaporation stage:
The liquid entering the heating chamber begins to heat up and boil under the action of heating steam (external fresh steam in the startup stage, and mainly secondary steam compressed by the compressor after normal operation). The generated secondary steam escapes from the surface of the liquid and enters the compressor. In the evaporation chamber, the steam and the concentrated liquid are separated by the separator, the concentrated liquid accumulates at the bottom of the evaporator, and the steam is sent to the compressor.
Vapor compression stage:
After the secondary steam enters the compressor, it is compressed to a higher pressure and temperature. The compressed steam returns to the heating chamber of the evaporator and continues to heat the liquid as heating steam, thereby realizing the recycling of steam. The operating parameters of the compressor (such as speed, compression ratio, etc.) will be dynamically adjusted according to the operating conditions of the evaporator and the required amount of heating steam.
Concentrate discharge stage:
As the evaporation process continues, the concentration of the concentrate at the bottom of the evaporator continues to increase. When the concentrate reaches the predetermined concentration or volume, the discharge pump discharges it from the evaporator. The discharged concentrate can be further processed according to the subsequent process requirements, such as crystallization, drying, etc.
Non-condensable gas treatment (if any):
During the evaporation process, some non-condensable gases may be produced, which will affect the performance of the evaporator. The non-condensable gases are usually extracted by a vacuum pump and processed in a condenser to separate the non-condensable gases from the steam to ensure the stability of the pressure and temperature in the evaporator.
Performance characteristics:
High efficiency and energy saving:
The biggest advantage of the MVR evaporator is its significant energy saving effect. Since it mainly relies on the recompression and recycling of steam to maintain the evaporation process, it can greatly reduce the consumption of external steam compared to traditional multi-effect evaporators and single-effect evaporators. In general, the energy consumption of the MVR evaporator is only about 30% - 60% of that of the traditional evaporator, which can save a lot of operating costs for the company when the energy cost is high.
Good environmental performance:
Due to its energy-saving characteristics, the MVR evaporator consumes less energy during operation, which correspondingly reduces the emission of greenhouse gases such as carbon dioxide. At the same time, through the effective evaporation and concentration of the feed liquid, the recycling and recycling of resources can be achieved. For example, when treating industrial wastewater, useful substances in the wastewater can be recovered to reduce the pollution of wastewater discharge to the environment.
High operating stability:
The control system can accurately adjust the operating parameters of equipment such as compressors and pumps, so that the MVR evaporator can operate in a relatively stable state. Even when parameters such as feed flow rate and feed liquid concentration change to a certain extent, it can adapt to these changes through automatic adjustment, maintain the continuity and stability of the evaporation process, and thus ensure the consistency of product quality.
Wide range of application:
It can handle a variety of feed liquids of different properties, including high salinity, high viscosity, and heat-sensitive solutions. For high-salinity solutions, such as brine concentration in the chemical industry, MVR evaporators can effectively separate salt and water; for high-viscosity solutions, good evaporation effects can also be achieved through reasonable equipment selection and operating parameter settings; for heat-sensitive solutions, since the evaporation temperature can be adjusted by controlling the steam pressure, the damage to the effective components in the solution can be minimized.
Application areas:
Chemical industry:
It is widely used in many fields such as salt chemical industry, fertilizer production, and organic chemical industry. For example, in the process of brine evaporation and crystallization, MVR evaporators can efficiently concentrate and crystallize brine to obtain salt products with higher purity; in chemical wastewater treatment, wastewater containing various organic and inorganic salts can be evaporated and concentrated to recover water resources and useful chemicals.
Food industry:
It is used for concentrated processing of foods such as juice, jam, and milk. Taking juice concentration as an example, MVR evaporators can concentrate juice at a lower temperature, well retaining the flavor and nutrients of the juice, while reducing energy consumption and improving production efficiency.
Pharmaceutical industry:
For the concentration of drug extracts, the MVR evaporator can operate under mild conditions to avoid the destruction of the active ingredients of the drug due to high temperature. For example, in the concentration process of Chinese medicine extracts, the efficacy of Chinese medicine is ensured to be unaffected by precisely controlling the evaporation temperature and pressure.
Environmental protection industry:
It is an effective equipment for treating high-salinity and high-concentration industrial wastewater. It can evaporate and concentrate wastewater to achieve wastewater reduction treatment, while recovering the salt and water resources in it to reduce pollution to the environment. In the treatment of landfill leachate, the MVR evaporator can also play an important role in evaporating the water in the leachate, reducing the volume of the leachate, and facilitating subsequent treatment.